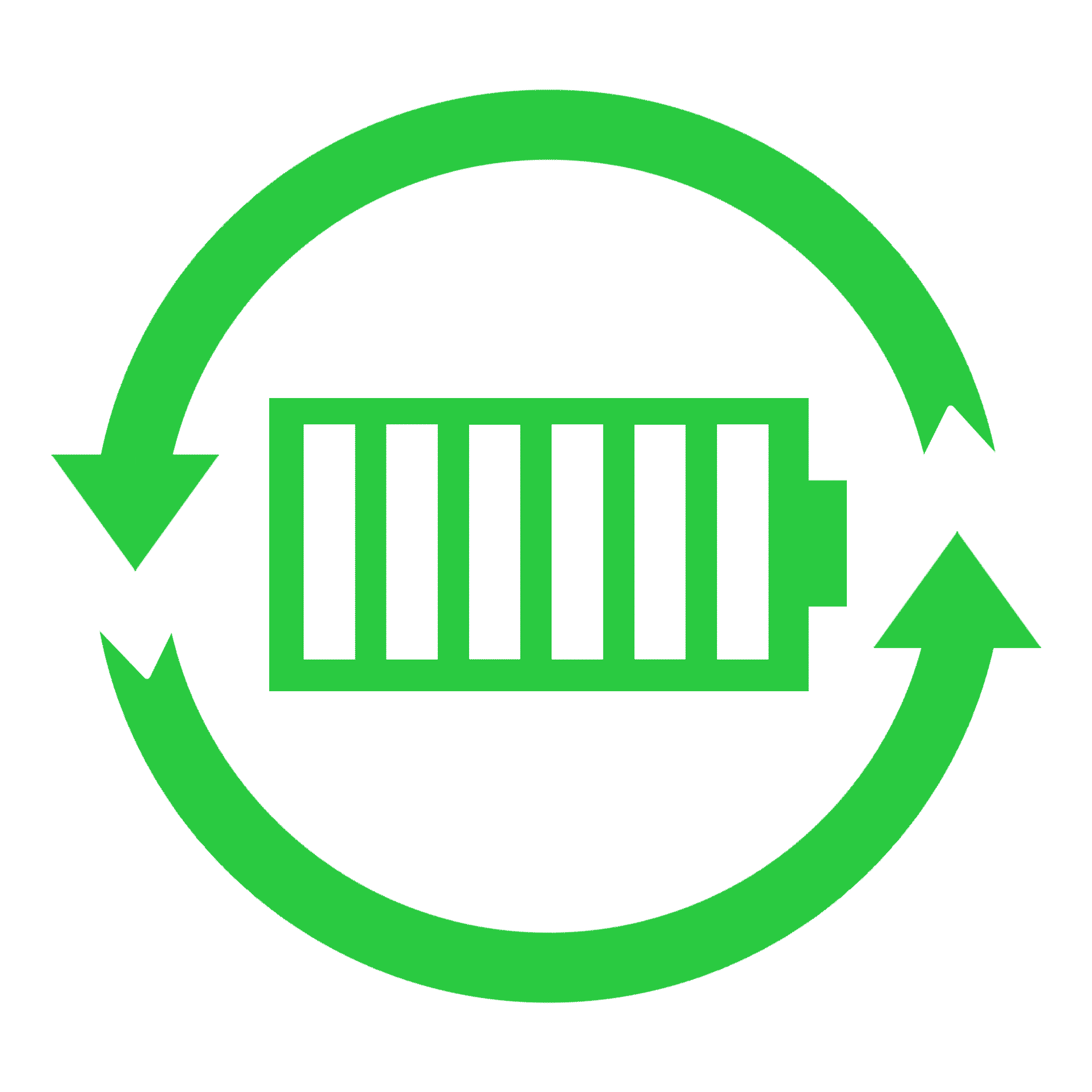
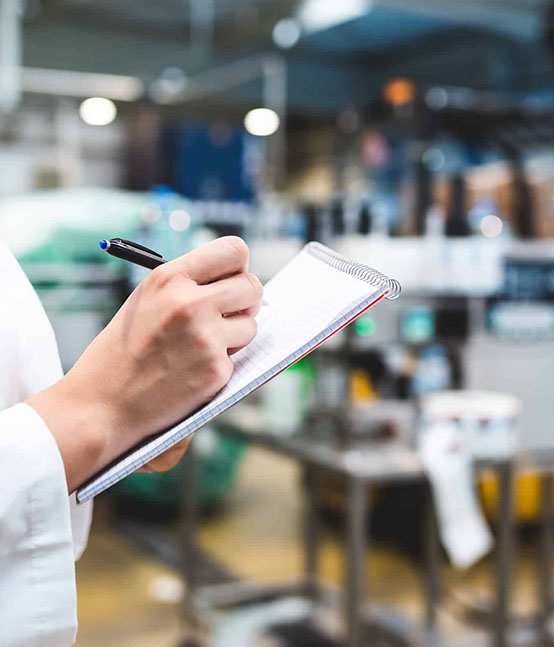
Setting New Standards: Unveiling Excellence in Quality and Control Operations
Our relentless pursuit of excellence is evident in every facet of our operations, especially in our meticulous Quality and Control (Q&C) department. Through strategic investments, advanced technology, and a steadfast commitment to quality assurance, we have met and exceeded industry benchmarks, setting new standards for product quality and safety performance.
-
1. Exemplary Product Quality
+Through rigorous quality control measures, we achieved a returns scrap rate of 0.455 ‰, surpassing the industry benchmark of 1 ‰. This remarkable achievement reflects our unwavering commitment to precision and excellence in every product we deliver. -
2. Industry-Leading Safety Performance
+Our products consistently demonstrate industry-leading safety performance, setting the standard for reliability and peace of mind. We prioritize safety at every stage of the manufacturing process, ensuring that our batteries meet the highest safety standards. -
3. Expert Team and Robust Infrastructure
+Our Quality Control Department is staffed by a dedicated team of professionals equipped with the expertise and resources to uphold the highest quality assurance standards.
A. Skilled Management Team: With 16 management positions established and 17 experienced personnel overseeing operations, our management team ensures the effective implementation of stringent quality control measures.
B. Thorough Inspection Capability: With 9 full inspection positions staffed by 29 diligent inspectors, we conduct comprehensive inspections to uphold product integrity and compliance with quality standards.
C. Continuous Training and Development: We prioritize the ongoing training and development of our employees. New hires undergo induction training while existing employees undergo regular assessments to maintain their qualifications. Key positions require approval from senior management before assuming duties. Our company's quality control department has 46 employees, accounting for 10.5% of total staff.
We are committed to continuous improvement to enhance product quality and customer satisfaction:
-
4. Investment in Key Processes
+We invest significantly in key processes, allocating resources to ensure stability and consistency. By maintaining a pool of multi-functional personnel, we mitigate risks and fluctuations in quality caused by personnel factors.
7. Acid charging process control
In 2019. Our acid filling and charging processes are also under strict control. All the acid charging machines have been modified to adjust the tooth distance, to be more accurate when adjusting the acid quantity on-site, and to reduce the standard tolerance of the acid quantity. Besides, we changed the single-tube acid calibration method from the original gravity acid to the vacuum acid, acid calibration method to simulate the operation of the equipment, so that the amount of acid needed to meet the standard requirements better.
-
8. Ultrasonic packaging process control situation
+When the product is ultrasonically capped, the company further strengthens the inspection of the product for polyacid and air leakage, i.e., the bonnet concave valve inspection before ultrasonically capping the product to ensure that all products that are not concave are singled out for re-processing confirmation.
At the same time for each team to pick out the non-dented valve battery, also be stipulated to require using different colors of markers to mark the non-dented valve single cell, to facilitate the non-dented valve battery for traceability and cause analysis.
To ensure the quality of product appearance, each packaging line has a full inspector for the appearance special inspection, to ensure that the product's appearance is quality qualified, a total of 45,325 batches shipped in 2022, and the customer did not feedback on bad appearance.
-
9. Test Chamber - Analytical Services Controls
+We have also set up a special test chamber - analysis of the control of the situation, the analysis of the defective products on the scene to deal with the treatment of still bad products for the cause of scrap analysis, to ensure that defective products can be analyzed promptly to find the cause of timely improvement, the company has arranged for the technical manager, R & D manager, improve the group manager rotation analysis of the scene every day to follow up on the analysis of the scrap every week by the manager of the duty to issue an “anatomical analysis of the report” to determine the reasons for the scrapping of each product belongs to the personnel operating problems, tooling/equipment problems, material problems, process problems or design problems, etc., to improve the direction of the improvement of the direction of clear to improve product quality.
Through daily sampling tests and daily scrap analysis, the company can quickly find out the problems of the products, the quality control department and then through the “Traceability Management Measures” of the traceability of the products, investigate and find out the problem points put forward to improve the requirements of the relevant departments responsible for the improvement, to stabilize product quality.
In 2023, the quality control department on-site product sampling test 4,572 times, all tests were strictly based on customer requirements, or far more than the same industry test conditions (reverse charging, side charging), and the customer did not feedback on product leakage, the customer did not feedback any batch of products batch of poor electrical performance.
-
10. Customer-Centric Approach
+Our commitment to quality extends beyond production to ensure customer satisfaction:
A. Timely Delivery: We guarantee 100% timely delivery, prioritizing efficiency and reliability to meet customer expectations.
B. Proactive Quality Management: Through rigorous testing, analysis, and traceability measures, we proactively manage quality to uphold our promise of delivering products of the highest quality and reliability, ensuring customer satisfaction and loyalty.
From our meticulous quality control processes to our proactive approach to customer satisfaction, every aspect of our Q&C department is geared towards delivering products of the highest caliber. With a focus on continuous improvement and innovation, we're not just meeting industry benchmarks; we're setting new standards for excellence.